Thermites are a double-edged sword. Packing a tremendous energy density, and eager to produce tremendous heat when ignited, thermite is great for welding train tracks. But sometimes you might be looking for a little more finesse. A new approach to 3D printing thermites might just be able to tame the beast.
Most of us do our soldering while sitting safely indoors in a comfortable climate. The biggest dangers we’re likely to face are burnt fingertips, forgetting the heat shrink, or accidentally releasing the smoke monster. But outside of our homes and workshops, there’s a lot of extreme joining of metals going on. No matter where it’s done, welding and brazing in the field requires a lot of equipment, some of which is unwieldy and even more difficult to move around in harsh conditions.
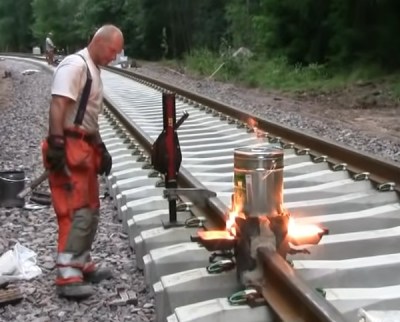
The utility of brazing is limited by all the complex scaffolding of hardware required to support it. This limiting factor and the discovery of thermite led to exothermic welding, which uses an energetic material to provide enough heat to melt a filler metal and join the pieces. Energetic materials can store a lot of chemical energy and forcefully release it in a short period of time.
Thermites are made of metal oxide and metal powder, often iron oxide and aluminium. When ignited by a source of high heat, thermite compounds undergo an exothermic reduction-oxidation (redox) reaction as the aluminium reduces the number of electrons in the iron oxide atoms. More heat makes the reaction run faster, generating more heat, and so on. The result is molten iron and aluminium oxide slag.
One of thermite’s first uses was connecting railroad tracks, and it’s still used for that purpose today. Here’s a great video of the thermite welding process in action.
Thermite is dangerous because it produces extremely high heat, but it has a lot of benefits. For one thing, it’s good at joining dissimilar metals. Although crimped connections are quite reliable, thermite joints are stronger and can withstand higher voltages. It’s easy to use for making lap joints — just make a solder sandwich with the work pieces, put thermite on top, and ignite it with magnesium ribbon or everyone’s introduction to pyrotechnics — a sparkler.
Thermite is predictably scalable, because the resulting heat output is directly related to the mass of thermite. Traditionally, the thermite reaction is tuned by varying the chemical composition — a little more rust, a little less aluminium powder until it does what you want. This is all fine and good, albeit a bit dangerous, in regular environments, like laying train tracks. In an austere environment like space, the ocean, or the battlefield, the danger of using high heat is much more pronounced.
A Printable, Programmable Heat Source
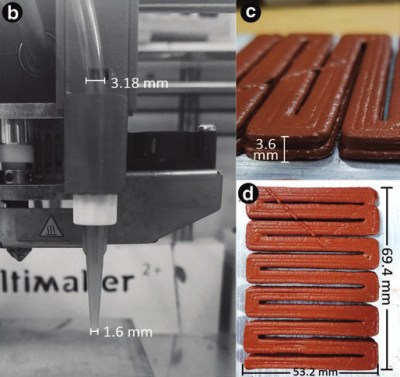
Recently, a mechanical engineering PhD student from Vanderbilt University created a printable 4D thermite paste that could make exothermic welding much safer, especially in austere environments.
This paste is made from iron oxide, aluminium powder, and gypsum powder. The gypsum powder binds the powders into a printable paste when mixed with water. Even though tartaric acid was added to the water, they had a scant 45 minutes to run it through the printer — a Discov3ry 1.0 paste extruder hooked up to an Ultimaker 2+. In their experiments, the team was successful in using the paste to fuse aluminium and make a simple copper lap joint.
By printing the paste in precise zigzags and other geometries they call reactive material architectures (RMAs), the team was able to exhibit more control over the thermite reaction. When distributed in these patterns, thermite behaves as a programmable heat source that burns more like a fuse and is inherently safer to store, transport, and use.
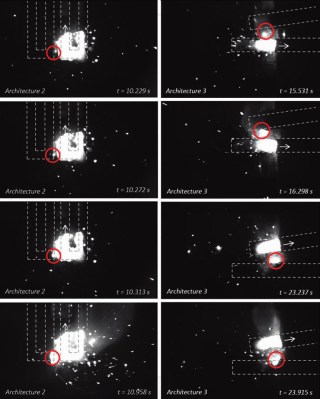
The shapes of these RMAs were chosen to explore the way that each would affect the thermite reaction. The first was a simplified zigzag, an elongated S pattern with hard right angles designed to measure the rate of propagation when one end is ignited.
The complex zigzag pattern above was designed to study the influence of ignited thermite to bridge the gap and ignite new sections that burn perpendicular to the initial reaction. The third architecture — a pair of simple zigzags placed parallel, but at a slight angle — was used to test thermite reaction propagation parallel to the starting reaction. All three architectures were printed and cured in forced-air oven, then ignited and filmed with a high-speed camera outfitted with a welding shade.
There are many joining applications that would benefit from such a controllable heat source. Thermite architectures for underwater or space welding could be designed and printed in advance and then ignited remotely, saving money, equipment expense, and potentially a few lives.
We’ve seen a few thermite hacks in our day, many of which were destructive rather than constructive. Since thermite isn’t something you can just pick up at the store, start by perusing recipes.
No comments:
Post a Comment