Everybody loves solar power, right? It’s nice, clean, renewable energy that’s available pretty much everywhere the sun shines. If only the panels weren’t so expensive. Even better, solar is now the cheapest form of electricity for companies to build, according to the International Energy Agency. But solar isn’t all apples and sunshine — there’s a dark side you might not know about. Manufacturing solar panels is a dirty process from start to finish. Mining quartz for silicon causes the lung disease silicosis, and the production of solar cells uses a lot of energy, water, and toxic chemicals.
The other issue is that solar cells have a life expectancy of about 25 years before they start dropping off in efficiency, which means that time is running out for all the panels that were installed during the early 2000s boom. The International Renewable Energy Agency (IREA) projects that by 2050, we’ll be looking at 78 million metric tons of bulky e-waste. The IREA also believe that we’ll be generating six million metric tons of new solar e-waste every year by then, too. Unfortunately, there are hardly any measures in place to recycle solar panels, at least in the US.
How are solar panels made, anyway? And why is it so hard to recycle them? Let’s shed some light on the subject.
How It’s Made: Solar Panels
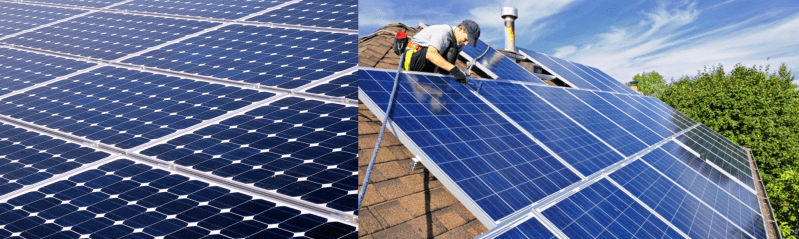
Solar panels come in three basic types — monocrystalline, polycrystalline, and thin-film. Each cell of a monocrystalline solar panel is made from a single silicon crystal. These are the single malt Scotch of solar panels, and are usually black.
Polycrystalline panels have a jumbled, multi-faceted look to them because they’re made from several silicon crystals. These panels are usually blue, and this is because of a coating that makes them perform better. Thin-film solar panels are the type you see in solar calculators and watches, and they offer the least efficiency. These are made from amorphous silicon, which is why they look so different from the other two.
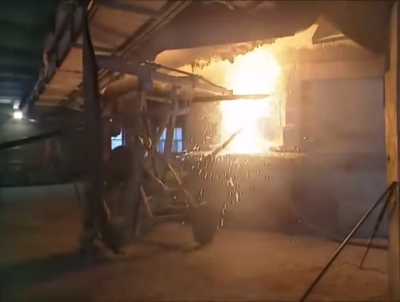
No matter the type, solar cells start with sand, usually high-purity quartz sandblasted at high temperatures. The quartz is first refined into metallurgical-grade silicon, then purified into polysilicon. This creates a highly toxic compound called silicon tetrachloride. This stuff is bad enough on its own, but when it gets dumped and reaches local bodies of water, it releases hydrochloric acid.
The resulting polysilicon is collected into rocks and melted together into ingots. Boron is added (known as doping) to give the silicon positive polarity. Then the ingots are sliced into paper-thin wafers that are coated with a substance that makes them absorb sunlight rather than reflect it.
The cells are treated with a phosphorus coating that negatively charges the surface, completing the p-n junction that makes it possible to convert the sun’s energy into electricity. The cells are baked in a furnace and then soldered together into panels. A layer of protective glass goes on the front, and a durable polymer goes on the back that keeps out dirt and debris.
So… Recycle Them?
If they are properly cleaned and maintained, solar panels can last for several decades. But as solar panels degrade, they become far less efficient, and eventually stop working altogether. The obvious solution might be to recycle all those solar panels, but it’s not that simple. People don’t go down to the big box store and buy solar panels directly, they buy them from companies who also install them. It’s left up to the companies to track the panels, take them back, and make sure they get recycled. The problem is that not everyone is aware that they can be recycled in the first place, and dumping them in landfills is not being policed much in the States.
Europe is really leading the way when it comes to e-waste recycling. The European Union have a law requiring that solar panel producers take back their panels at end of life and recycle them. Britain has a refinery that uses microbes instead of cyanide to break down e-waste and extract the precious metals. And France is home to Veolia, the world’s only commercial-scale photovoltaic recycling plant. In 2017 their partner PVCycle collected 2,400 tons of end-of-life panels throughout France. Veolia says they are able to achieve a 95% rate of re-usability for the collected metal and glass. Check out their process in the video below.
In the US, there are no federal mandates for recycling solar panels, and only Washington state and New York have any kind of laws about them. As a result, only about 10% of American panels are recycled. The other 90% get shipped to countries without mandates for reuse, or end up in landfills, leaching lead and other toxic chemicals into the Earth.
Right now in the US, recycling solar panels is difficult, and recovering the silver, copper, and silicon requires custom solutions. Scrapping the aluminum frames and silver from the metallization paste doesn’t net that much, and it costs $12-25 per panel plus transportation costs to recycle them. Dumping them in landfills only costs about $1 per panel.
It’s hard to compare the damage done by the solar panel manufacturing process to the damage caused by burning fossil fuels for energy. Neither one is good, so are we solving one problem while creating another? If we don’t figure out a global scheme for recycling panels, we’re certainly headed for a crisis.
No comments:
Post a Comment