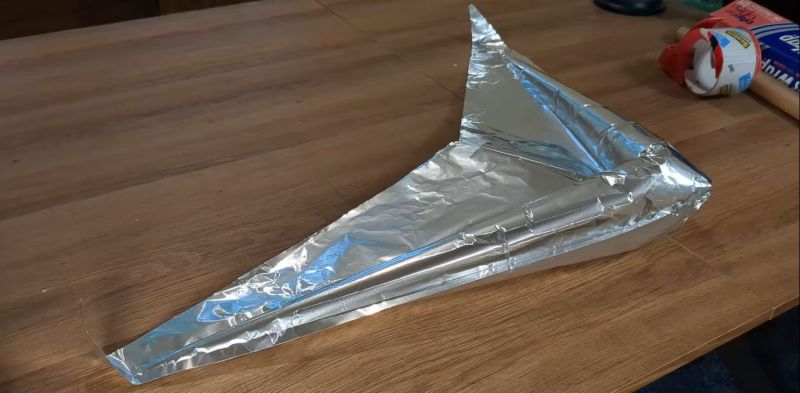
Hydroforming is a very effective way to turn a ductile metal like aluminium or stainless steel into a specific shape, either using a die or by creating a closed envelope in which the hydraulic fluid is injected. While trying to think of ways to create a hydroformed airplane without spending big bucks on having it done professionally – or learning to weld sheet metal together with waterproof welds along the seams – [Adrian Perez] decided that using plain aluminium foil as found in the average kitchen might be a good way to get his feet wet here. When stuck together with double-sided tape, the foil is both strong and light enough to be inflated like a party balloon and still fly better than a lead balloon (which do fly, albeit poorly).
The basic design for the initial Luma glider that he assembled is based around a Kline-Fogleman (KA) airfoil. This type of airfoil is mostly characterized by the simplicity of construction, having been devised in the 1960s for paper airplanes. It uses a stepped approach rather than a continuous airfoil and has seen mostly attention in hobby circles. Even if this Luma glider brings to mind the ill-fated Goodyear Inflatoplane, a hydroformed version of these foil prototype gliders would not have to rely on being inflated to function.
For small-scale prototypes, using low-cost aluminium foil or similar to test out shapes before committing to a design to be welded and hydroformed does seem like a useful approach.
No comments:
Post a Comment