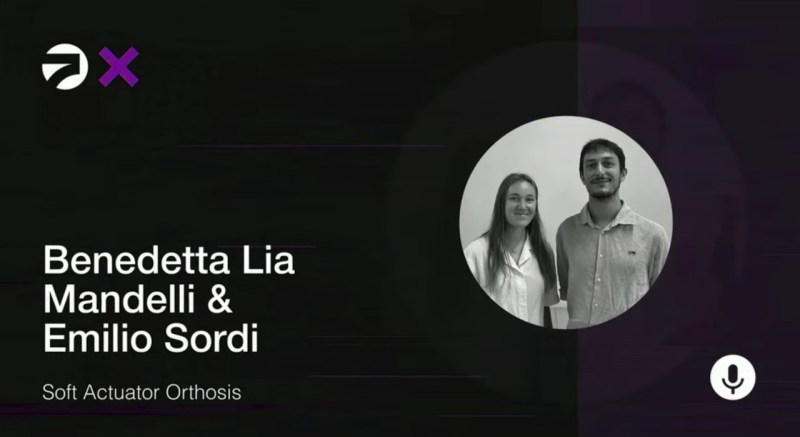
When we think of assistive prostheses or braces, we often think of hard and rigid contraptions. After all, it wasn’t that long ago that prosthetic limbs were still being made out of wood. Even devices made of more modern materials tend to have a robotic quality that inevitably limits their dexterity. However, advancements in soft robotics could allow for assistive devices that more closely mimic their organic counterparts.
At Supercon 2023, Benedetta Lia Mandelli and Emilio Sordi presented their work in developing soft actuator orthosis — specifically, a brace that can help tetraplegics with limited finger and thumb control. Individuals with certain spinal cord injuries can move their arms and wrists but are unable to grasp objects.
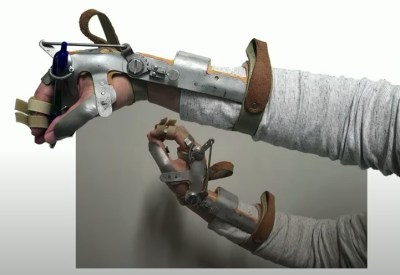
Existing braces can help restore this ability, but they are heavy and limited by the fact that the wearer needs to hold their wrist in a specific position to keep pressure on the mechanism. By replacing the rigid linkage used in the traditional orthosis, the experience of using the device is improved in many ways.
Not only is it lighter and more comfortable to wear, but the grip strength can also be more easily adjusted. The most important advancement however is how the user operates the device.
Like the more traditional designs, the wearer controls the grip through the position of their wrist. But the key difference with the soft actuator version is that the user doesn’t need to maintain that wrist position to keep the grip engaged. Once the inertial measurement units (IMUs) have detected the user has put their wrist into the proper position, the electronics maintain the pressure inside the actuator until commanded otherwise. This means that the user can freely move their wrist after gripping an object without inadvertently dropping it.
From Concept to Production
While much of the talk covers the advantages of their brace, the team also goes over how their design was improved from their original proof of concept work — which featured an earlier version of the soft actuator literally zip tied to the wearer’s fingers.
While the brace itself was modified, the biggest changes came to the actuator itself. The first version used two chambers, but this was eventually simplified to just one. In addition, they switched from using a pneumatic system to hydraulic. Originally, an air pump was used to pressurize the actuator, but they found a syringe pushing liquid into the actuator provided better control.
Soft Actuator Design
Perhaps one of the most interesting aspects of their talk was the discussion of the soft actuator itself. In a series of slides, they described not only how the mechanism works, but how they produce them in-house using a surprisingly simple process.
Essentially, the actuator is a strip of silicone with a series of hollow chambers molded into it. When the actuator is pressurized with air or liquid, these chambers expand. Normally, this would just make the structure blow up like a balloon, but by integrating a non-elastic layer onto the bottom of the actuator, it instead causes it to curve around. Once the system releases pressure, the silicone naturally returns to its original size and shape.
Creating the actuator is as simple as pouring silicone into a custom-made mold, and then attaching a strip of cotton to one side with a bit more liquid silicone. Once cured, they cut cotton to size and the actuator is ready to go. While the team tested several shapes for the actuator, the final version is a simple rectangle, as this was determined to be the easiest to produce.
Looking Ahead
While the design is already impressive, it’s still essentially a prototype. The electronics still live on scraps of protoboard, and the team continues to research potential improvements to their actuator design — from changes to the silicone mold to different motor and gearbox options for driving the syringe. Benedetta and Emilio also want to look into different ways of controlling the actuator outside of their current IMU solution.
Ultimately, they hope to put the brace into production as a semi-assembled kit that can be put together and fitted to the wearer by a medical professional in the field. The hope is that by bringing the cost of the brace down and making it easy to customize for the individual, they can bring this assistive technology to traditionally underserved areas.
No comments:
Post a Comment